Intelligence and efficiency on your manual and repetitive assembly line
Manual and repetitive assembly can lead to several problems and losses for companies, especially in the automotive and manufacturing industry. Some of the challenges associated with manual and repetitive assembly include:
- Defective products, rework, and additional repair costs: the repetitive nature of manual work can increase the risk of assembly errors, even with experienced workers.
- Injuries and workers' health problems: repetitive work can lead to musculoskeletal injuries. In addition, the constant repetition of movements can cause fatigue and stress, impacting on workers' physical and mental health.
- Lower productivity and efficiency: manual assembly is often slower and less efficient than automation. This can result in lower productivity and production capacity, which can negatively affect companies' profitability.
- Rework and warranty costs: defective products resulting from manual assembly may require rework or repair, increasing production costs and warranty costs for the company.
- Fines and penalties: in regulated sectors such as the automotive industry, errors in manual assembly can lead to non-compliance with safety standards and government regulations.
A notable example related to errors in manual assembly occurred with Ford Motor Company in 2020. Ford issued a recall for around 2.5 million vehicles in the United States due to a problem with the ignition switches. This was due to a defect in the manual assembly of the ignition switches.
Defective ignition switches posed an accident risk, as they could unexpectedly switch off the vehicle's engine, depriving the driver of power-assisted steering and power-assisted brakes. This could lead to a loss of control of the vehicle and increase the risk of collisions.
Ford identified the problem through consumer reports and internal investigations. After confirming that the defect was related to the manual assembly of the ignition switches, the company issued the recall to correct the problem in all affected vehicles by replacing the faulty ignition switches.
This case highlights how errors in manual assembly can have serious consequences, yet all this damage can be avoided with the solution brought to Europe by Macnica ATD Europe, Retrocausal.
This platform monitors manual and repetitive assembly workstations in real time.
It then identifies whether the process is correct, optimizing quality control.
Intelligent solution for employee training
Using Artificial Intelligence, Retrocausal guides employees in real time to minimize manual and repetitive assembly errors.
In the image below, you can see the Retrocausal system running and alerting the employee to a cable that has not been connected as it should. Alerts can also be made in a variety of ways, for example, by showing a monitor/display in front of the operator, a lighting device, an audible alert, or a multimedia projector.
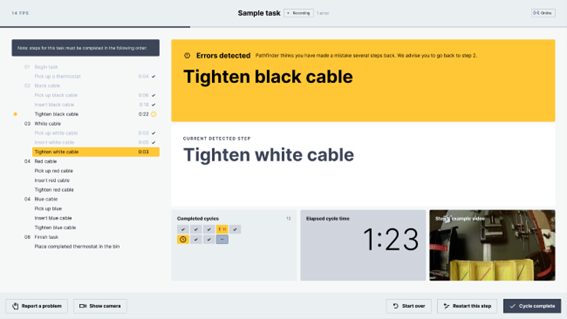
Retrocausal works like an extra pair of eyes on a manual, repetitive assembly line.
With a single camera, a computer and artificial intelligence, the Retrocausal solution enables constant monitoring and error detection in manual and repetitive assembly.
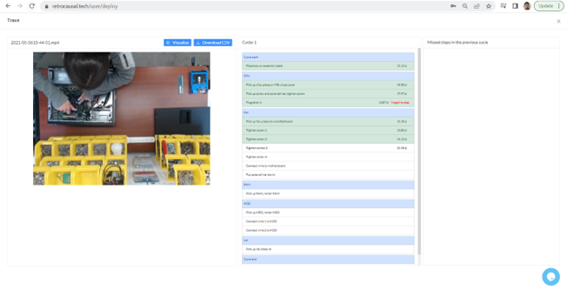
In addition, it issues alerts immediately when it identifies possible faults, such as forgetting to tighten a screw or connect a cable, thus guaranteeing precision, production quality and quality control.
This type of error in manual and repetitive assembly can be more common than you think, especially at the start of training a new employee or at the end of an exhausting working day, causing rework or even the loss of the product, not to mention the loss.
In addition to avoiding these problems, Retrocausal's artificial intelligence solution has an excellent cost-benefit ratio (ROI), as it speeds up training and guarantees a high level of quality for products that go through manual and repetitive assembly.
To find out more about the Retrocausal solution and other Macnica ATD Europe technologies that will help increase the efficiency of your production, contact us.